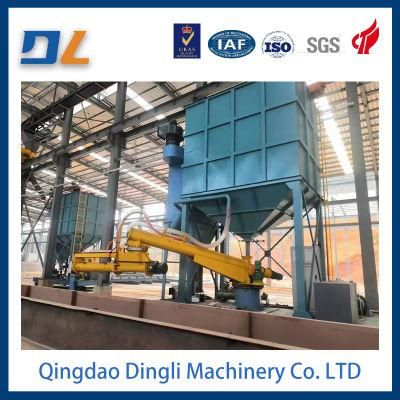
High Quality Resin Sand Recovery Equipment
Qingdao Ding Li Machinery Co., Ltd.- After-sales Service:After-Sales Service
- Warranty:One Year Warranty,
- Control Type:PLC
- Customized:Customized
- Condition:New
- Automatic Grade:Automatic
Base Info
- Model NO.:5t,h
- Certification:CE, RoHS, GS, ISO9001
- Type:Sand Casting
- Transport Package:Container
- Trademark:DL
- Origin:Qingdao, China
- HS Code:8474802000
- Production Capacity:800
Description
Basic Info.
Model NO. 5t/h Certification CE, RoHS, GS, ISO9001 Type Sand Casting Transport Package Container Trademark DL Origin Qingdao, China HS Code 8474802000 Production Capacity 800Product Description
Qingdao Dingli machinery Co., Ltd. is located in the beautiful seaside - Qingdao Pingdu, the company set scientific research, manufacturing, installation and commissioning, after-sales service in one. Mainly produces resin sand production line, clay sand production line, coated sand production line equipment, all kinds of sand processing single equipment. The company has advanced casting machinery manufacturing and development technology, the production of products can fully meet the international and domestic market demand. The company has excellent design and development team, skilled construction team, domestic leading casting equipment design concept, perfect after-sales service system, willing to cooperate with the majority of casting enterprises, create a better tomorrow.In line with the "down-to-earth, integrity-based, pay attention to service, continuous innovation" business philosophy, through continuous efforts. With our own efforts and focus on the development of a series of perfect processing equipment, to meet the different needs of the majority of users.
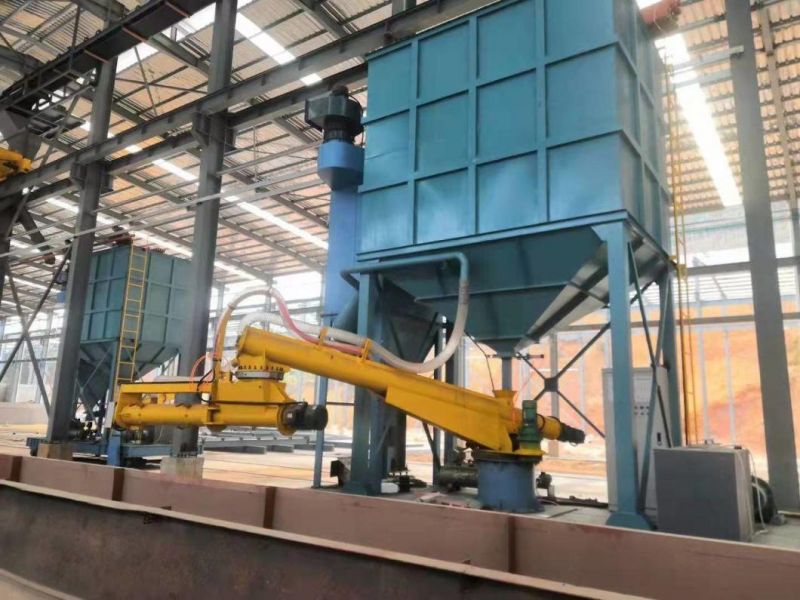
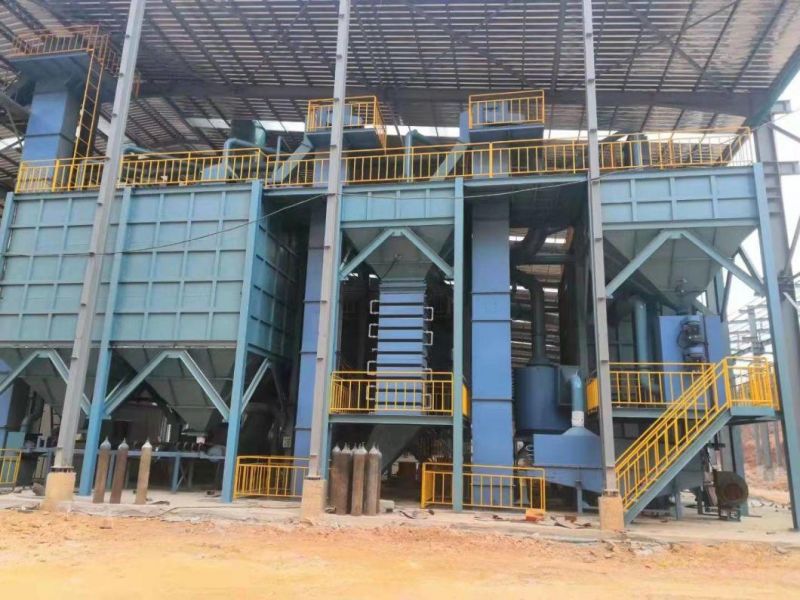
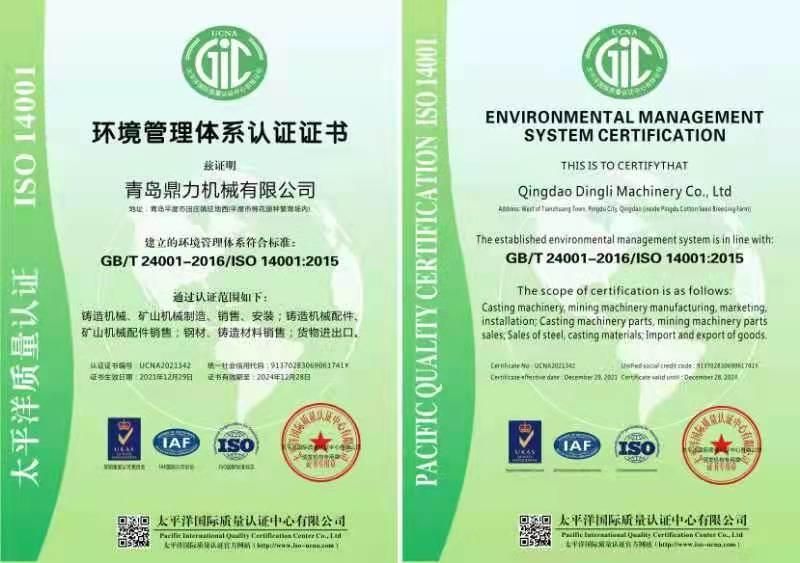
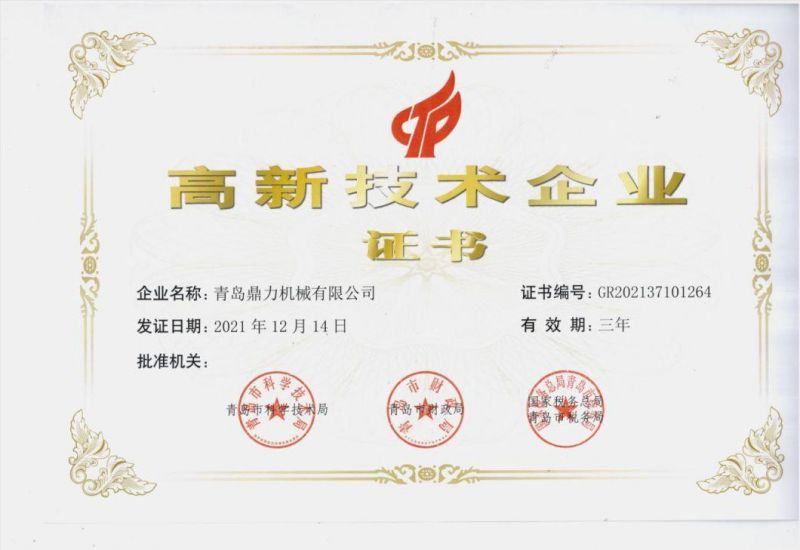
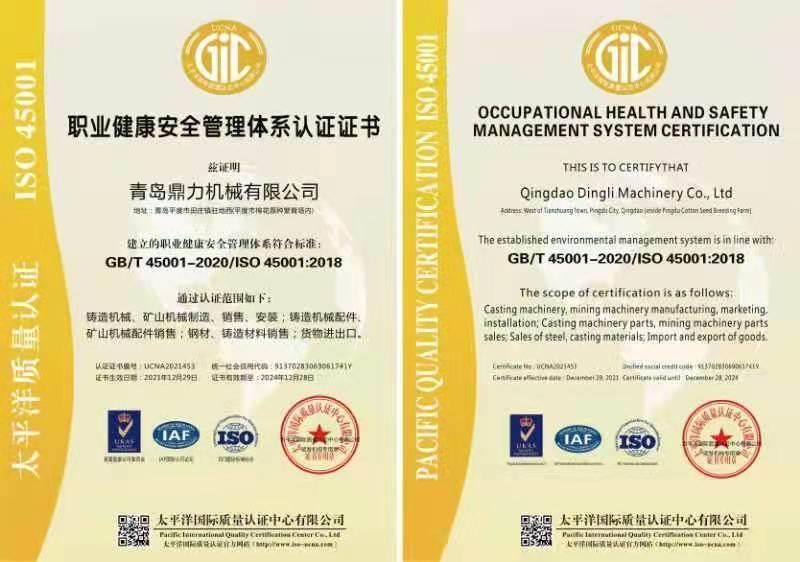
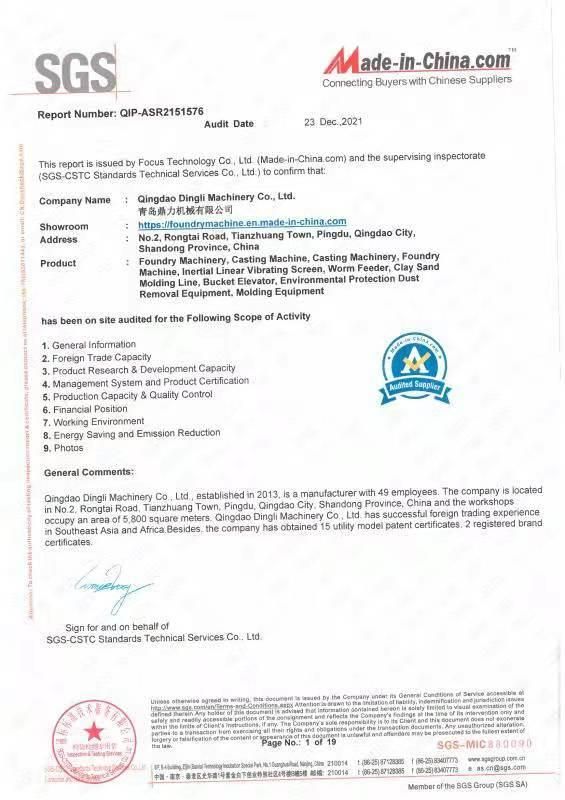
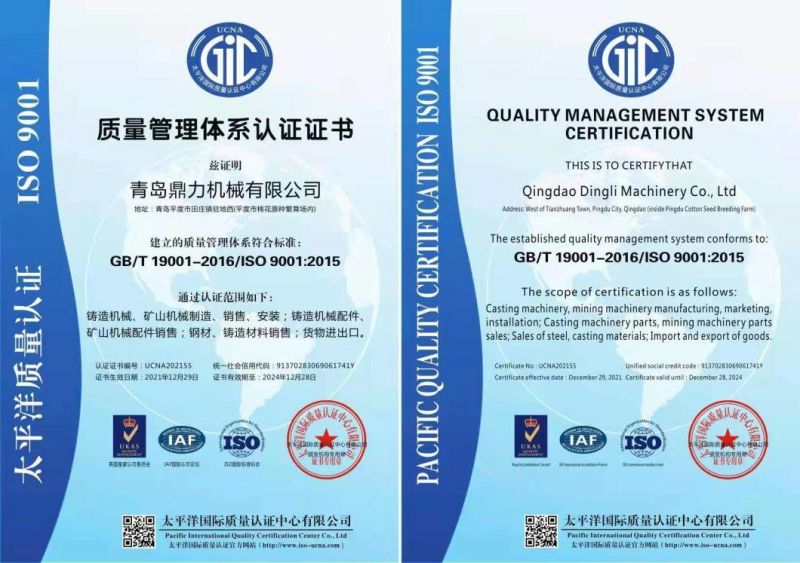
1. Advantages and disadvantages of furan resin sand
1.1 the advantages
1) The casting has high dimensional accuracy and clear external contour; Casting surface smooth, good appearance quality; Compact structure and high quality casting.
Because the resin sand has good fluidity, easy to tighten, demolstering time can be adjusted, high strength after hardening, no deformation in the subsequent handling and box closing process; Because of the high stiffness of resin sand, basically invisible wall displacement phenomenon in the pouring and solidification process, so the dimensional accuracy of the casting is high, it can be improved 1-2 levels than the castings produced by clay sand and oil sand.
2) No drying, shorten the production cycle, save energy.
3) the drying process is omitted, the sand is easy to tighten, the collapsibility is good and easy to clean, etc., which greatly reduces the labor intensity of workers and creates conditions for the realization of mechanized production.
1.2 Deficiencies
1) High quality requirements for raw sand;
2) Modeling and pouring site, in the production process there is a pungent smell.
3) Resin sand production, high cost, should be considered comprehensively.
As can be seen from the above, the advantages of resin sand are more prominent, so it has been promoted and applied in China.
2. Production technology of furan resin sand
2.1 Selection of raw materials
1) Requirements for sand for casting
The raw sand has a great influence on the properties of furan resin sand and the amount of binder and the surface quality of casting, so it is required that the content of SiO2 in the raw sand should be high, and the mud content and acid consumption value should be low. Size: large pieces 42 or 30 groups, medium pieces 21 groups, small pieces 15 or 10 groups.
2) Furan resin
Furfuryl alcohol containing resin known as furan resin, its higher furfuryl alcohol content, resin storage performance can be improved, high thermal strength but increase the cost. Free formaldehyde in resin is the source of irritant gas in production, but also one of the factors to deteriorate the environment, should be controlled. Cast iron production should choose low nitrogen or nitrogen free resin, practical application according to the technical requirements and structure of the casting to choose.
3) curing agent
Organic sulfonic acid solution is generally used to adjust the curing speed according to the concentration of its aqueous solution or alcohol solution.
4) additive
In order to improve the properties of furan resin self-hardening sand, some additives are often added in the ratio. Adding a small amount of silane as coupling agent can obviously improve the strength of resin sand, but with the extension of time, the effect gradually decreases, generally will disappear in two months. Therefore in the domestic by the user before use to add and stir evenly, should be used up as soon as possible.
2.2 Recycling of furan resin self-hardening sand
The good recovery and regeneration of furan resin sand is one of the major advantages. How to control the quality of recycled sand is the key to produce high quality resin sand castings.
1) Sand temperature regulation
Sand temperature stabilization is the key to furan resin self-hardening sand, so sand temperature regulation is essential, especially the sand temperature of reclaimed sand. If the sand temperature can be controlled well, it can improve production efficiency, reduce sand damage and casting defects, and can reduce the number of beads added, reduce costs, improve the working environment.
2) Quality indicators of reclaimed sand
Burning and gas emission
The amount of burning is a rough standard to measure the residual amount of hardened binder in resin sand mold. With the increase of reuse times, its growth rate gradually decreases, generally after 10 ~ 15 cycles can reach a stable value. Cast iron production can be controlled within 2.5%. There is almost a straight line relationship between burning volume and gas emission, and gas emission can be calculated by burning volume. The porosity defects of castings can be effectively prevented if the particle size distribution and the content of fine powder are well controlled.
Acid consumption value and PH value
For furan resin with acid as curing agent, the acid loss value is usually negative. If PH value is too high, it is difficult to determine the appropriate amount of acid curing agent, and the general PH value is controlled in the range of 3 ~ 6.
3) After repeated use of reclaimed sand, sand is easy to fine grain, which will affect the air permeability of molding sand. More attention should be paid to the production process.
2.3 Mixing process
1) Proportioning and mixing
A mixture ratio
The addition of furan resin generally accounts for 0.8 ~ 1.5% of the sand weight, and the addition of curing agent accounts for 20 ~ 70% of the resin weight, according to the seasonal temperature changes to adjust.
B Blending process
Modeling is best to use continuous sand mixing machine mixing system. It is generally mixed with the original sand, reclaimed sand, curing agent and resin in turn. When using intermittent sand mixing machine, sand should be added first, curing agent should be carefully added after starting the sand mixing machine, resin should be added after mixing for 1 ~ 2min, and sand should be unloaded immediately after mixing. Core making using bowl type sand mixing machine (intermittent), according to the size of the weight of the core to choose more and less mixing.
2) hardening process
The hardening rate of resin sand is greatly related to sand temperature, ambient temperature, air humidity and the type and amount of curing agent.
A temperature
The temperature of the raw sand is best controlled at 20 ~ 35ºC. If the temperature of the raw sand and the working environment is too low, the hardening rate will become very slow, delaying the demoulding time and reducing the production efficiency. But the temperature is too high, the use time is too short, the fluidity of sand becomes poor, affecting the core compaction. Therefore, the hardening rate should be well controlled, and the usable time and demoulding time of resin sand should be reasonably controlled.
B Curing characteristics
The ratio of available time and demoulding time is used to represent the curing characteristics of the binder. The larger the ratio is, the better the curing characteristics of the curing agent are, generally 0.3 ~ 0.5.
3. Casting process design and production site process control
3.1 Process Design
1) The mold Angle should be larger than the clay sand
Resin sand core in the mold, has a certain hardening strength, almost no concession, the friction is larger when the mold, generally can not be used to knock shape or core box frame loose shape to mold. Therefore, in the production of appearance, should be appropriate to increase the drawing Angle, to ensure the appearance of quality, in order to facilitate the mold.
2) The process design should give full consideration to the characteristics of self-hardening sand and minimize the live blocks. It is better to cancel the live blocks if the sand core can be used to improve the production efficiency.
3) Sand box design
Taking advantage of the characteristics of high strength of resin sand after hardening, and under the premise of satisfying the effective sand feeding quantity (according to the size and complexity of casting, the sand feeding quantity can be selected between 30-100mm), the size of sand box can be reduced, the sand-iron ratio can be reduced, and the production cost can be reduced.
4) Pouring and riser system design:
(1) The principle of the design of pouring riser is: less feeding riser should be set, more air and overflow riser. Because of the resin sand mold stiffness, casting strength is high at the beginning of casting, there are conditions to use the graphitization expansion of cast iron solidification process, effectively eliminate shrinkage cavity, shrinkage porosity, to achieve less riser or no riser casting of gray cast iron, ductile cast iron castings.
Try to avoid the concentrated opening of the gate at the riser, should improve the slag and filling capacity under the premise of the use of scattered, radial introduction of overflow, the end face of the transverse gate is high trapezoid, the opening principle of the inner gate is short, thin, wide; The centrifugal slag collecting bag is preferred to change the cross-section shape of the end area of the runner to prevent the suction of the runner and the secondary oxidation of liquid iron.
(3) For the production of heavy castings, the casting system shall give priority to the use of ceramic tubes to prevent the sand hole defects caused by sand washing.
5) Compared with clay sand, processing allowance can be appropriately reduced and machining efficiency can be improved.
3.2 Site process control
1) The modeling process is best to use the shaking table to improve the compactness of the casting, to ensure the geometry of the cavity and the dimensional accuracy of the casting.
2) to strengthen the core of the exhaust, more air outlet and airway, in the pouring process to ensure that the gas in the core out of the type in time.
3) it should be noted that the mold core should not be immediately on the coating, so when the resin hardening reflection is still in the early stage, if the water in the water-based coating will affect the normal hardening; If brush alcohol-based coating immediately lit will also not reflect the resin over burning, affecting the surface temperature of the core.
4) summer wet season production, it is best to carry out dry treatment of resin sand to remove moisture, to prevent the occurrence of stomatal defects caused by "choking". After the casting molds are stored for hours, they can be poured into the box.
5) Material control of resin sand casting: the insulation property of resin sand should be fully used, and measures should be taken in the production process to ensure the quality of material.
Gray cast iron:
Gray cast iron casting resin sand casting material, because of its unique heat preservation, generally decreased 0.5 ~ 2 brand, production should be according to the actual wall thickness and size of casting flexible control.
Nodular cast iron:
By making use of its heat preservation property, adopting the process method of heat preservation by pressing fire and prolongating the working time, the ductile iron castings (such as QT400-18 and QT450-10, etc.) dominated by ferrite can be stably produced in the as-cast condition. However, in the production of pearlite ductile iron and anti-wear ductile iron castings (such as QT600-3, QT700-2, etc.), special process should be adopted to ensure that.
(3) In the production of ductile iron, attention should be paid to the occurrence of bad spheroidization phenomenon, which is related to the use of sulphonic acid curing agent sulfur infiltration, prevention measures to appropriately increase the dosage of spheroidization agent, so that the residual Mg of liquid iron in 0.045 ~ 0.055.
4. Defect analysis and countermeasures of resin sand casting
Compared with other sand types, furan resin sand has the advantages of fewer casting defects, low scrap rate, high dimensional accuracy of casting, clear surface and clear outline, but if the site is not used properly, there will be quality problems, sometimes even cause batch scrapped.
4.1 hole:
There are two main types:
One is because of resin sand gas, gas too late to discharge the formation of invasive pores;
The second is the compound containing nitrogen in the resin. After pouring, the decomposed atomic nitrogen and hydrogen enter the liquid iron, and the gas dissolved in the condensation is too late to precipitate, forming pinholes. For cast iron parts, the prevention measures are to reduce the amount of resin added under the condition of meeting the strength of molding sand; Furthermore, strengthen the core exhaust, pay attention to ignition when pouring air.
4.2 adhering sand:
The reason is that the resin is decomposed at about 500ºC, the resin mold is ablated, the sand gap is increased and the bond is lost, and the molten iron penetrates into the sand.
Prevention measures are:
(1) Increase core compactness;
(2) the thick wall can use special raw sand such as zircon sand chromite sand and cold iron;
(3) brush refractory coating and appropriately reduce pouring temperature;
(4) Select the appropriate type of furan resin.
4.3 cracking:
When casting thin-wall castings, the resin sand mold can not be burned through, forming a solid layer of coking residual carbon layer, preventing the casting shrinkage, resulting in thermal cracks. Because the production can not pursue high sand strength, core hollow structure, casting can be filled with sand block or embedded plastic good material, improve the concession of sand.
productivity(t/h) | 5 |